Supply chains have always been sensitive to global changes, and the vulnerability of today's supply chains is shifting traditional methods toward new principles and goals for multinational companies. In recent history, supply chains have come into the spotlight worldwide as the COVID-19 pandemic disrupted the global order, raising questions for international players. As a result, mass factory closures, trade wars, tariffs, and invasions in Europe, such as the conflict in Ukraine, growing inflation, and severe weather events, have created an uncertain environment. These disruptions have shown that disturbances are no longer isolated events. During the pandemic, fluctuating supply from certain companies led to unstable purchasing, complicating planning and production. This further resulted in port congestion and a global shortage of containers.
According to a recent study conducted by FMI (Future Market Insights), the revenue of the global supply chain management market is expected to reach approximately $25.7 billion in 2023, growing to $78.5 billion by 2033, with a CAGR of 11.8% from 2023 to 2033. Despite the projected growth, it is undeniable that supply chains are facing another year of instability and inflationary pressure, prompting leaders to reconsider traditional global supply chain models. As the times become more uncertain, companies must make their supply chains more cost-effective, resilient, and sustainable. Extreme volatility is the new global reality. Given all these developments, the need to build supply chain resilience has never been greater. It is a crucial objective for many companies in their business strategies for the foreseeable future. Another priority is agility, allowing companies to respond to rapidly changing consumer needs. Sustainability is also a significant focus, as supply chains are crucial in transitioning to a clean and socially just economy.
Research from a global institute indicates that companies experience a supply chain disruption lasting one to two months, approximately every four years on average. In the consumer goods sector, the negative financial consequences of these disruptions over a decade can amount to 30% of one year's EBITDA. In 2011, following the devastating earthquake and tsunami in Tohoku, Toyota experienced a six-month reduction in production capacity. However, this did not prevent the automaker from altering its production strategy by regionalizing supply chains and paying particular attention to supplier vulnerability. When another major earthquake struck Japan in April 2016, Toyota resumed production within two weeks. During the early stages of the COVID-19 pandemic, sportswear manufacturer Nike developed a logistics program to track products going through outsourced production. They also used demand forecasting analytics and redirected inventory from retail to digital sales channels. With these measures, Nike limited the sales decline in the region to just 5%, demonstrating that digital solutions can provide companies with a competitive edge even in crises.
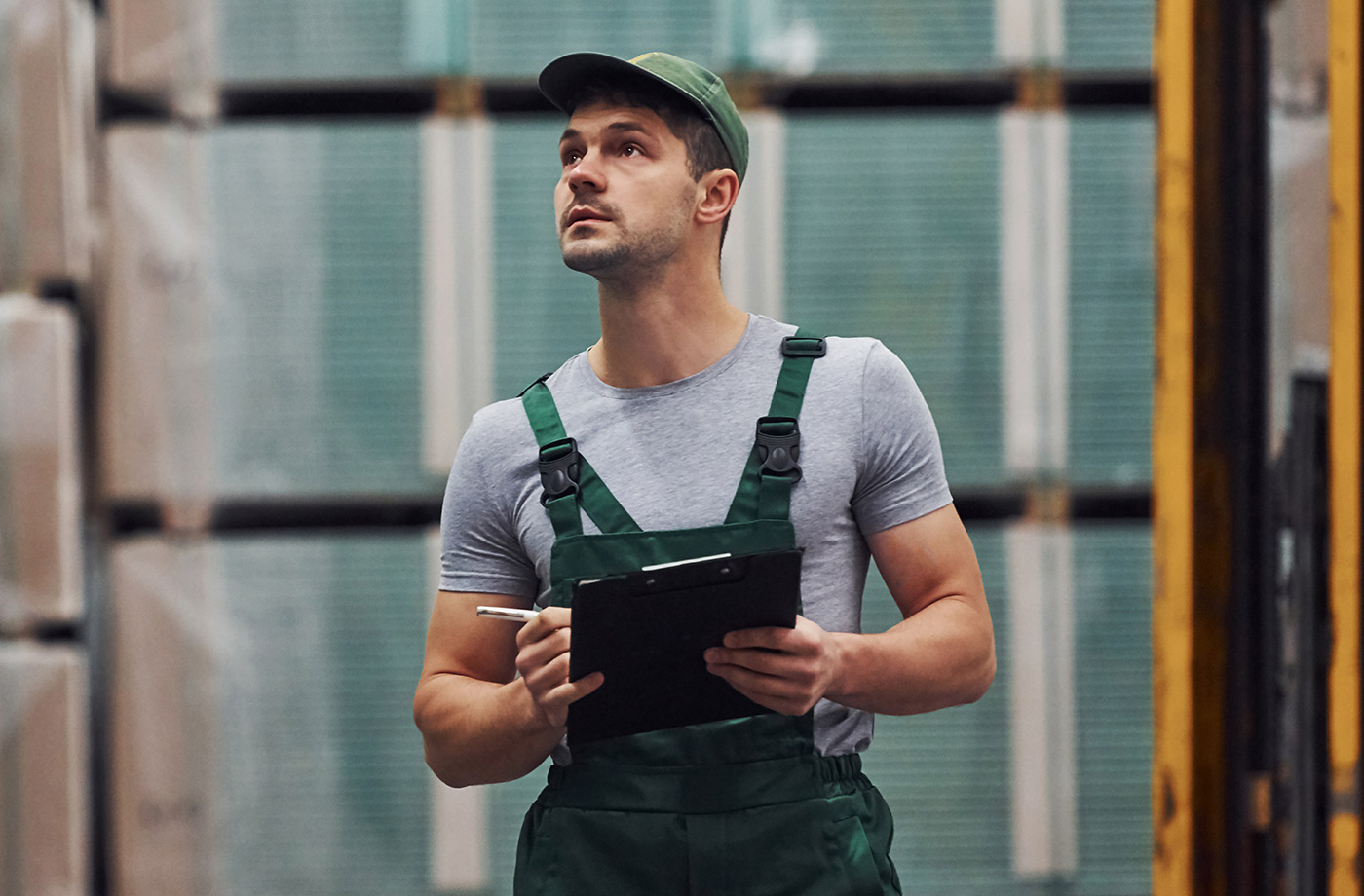
Despite companies being aware of the importance of the supply chain in maintaining the global economy, there is an evident lack of investment in what is sometimes referred to as the "first mile," meaning the first 90 days from the moment an order is placed with a supplier to the moment it is delivered. This phase significantly influences the product's outcome. A great example of global best practice is Zara, which demonstrates how a technologically integrated supply chain can quickly move products from sales locations to designers, then to production and logistics, repeating the entire process repeatedly. This retail giant changes its clothing designs every two weeks compared to the industry standard of three to four months and consistently achieves outstanding profit results year after year. Zara has built its technology by developing digital supply chain integration, from planning to delivery. A digital, interconnected, and automated supply chain is the foundation for improvement. Linking supply and demand is crucial for a company to gain more control over profit and sales, reduce purchasing costs, and create visibility for sales throughout the entire process. While historically seen as a nice-to-have luxury, technology is now an imperative for every importer. The goal is to digitize the procurement process fully, establish connectivity between internal teams, suppliers, and partners, and implement automation to minimize redundancies and errors.
As a mega-trend for 2023, sustainability will take up a significant portion of supply chains as companies aim to achieve specific ESG (Environmental, Social, and Governance) goals from an internal and global perspective. Many companies are making business decisions based on sustainable management with other stakeholders along the supply chain, meaning sustainable supply chains and green logistics are becoming necessary. What was once a trend has become essential as data management and technology providing greater logistics transparency are introduced into supply chain processes. Such innovations bring many benefits, including more accessible access to insights into significant data that play a crucial role in decision-making and other proactive initiatives. Over the past year, a key trend for many logistics companies has been investing in a cloud-based digital transformation strategy, and this trend will accelerate this year as companies leverage technology to mitigate inflationary pressures and global economic slowdowns. New priorities like resilience, agility, and sustainability cannot be applied to existing supply chain setups. They must be built from the ground up and considered in every supply chain design, organization, and operation element. For many companies, this will likely require a change in the mindset of top management, where, in addition to traditional cost-focused methods, capital utilization, service, and quality, they also consider resilience, agility, and sustainability. To succeed in all six dimensions, workforce management and the implementation of digitalization will be essential.
Lately, the supply chain has received chiefly negative attention. Companies worldwide have experienced business disruptions due to the vulnerability of their supply chains. They have learned harsh lessons about supply and demand instability, pondering control, transparency, and regionalization issues. The lack of resilience has become apparent, prompting a call to action for companies worldwide to prepare for future events. Many see 2023 as a year of correcting mistakes, an opportunity to leverage first principles for redesigning supply chains that allow growth. However, the question that remains is whether companies are simply reverting to old practices and hoping not to be threatened the next time a global event occurs (and there is a high likelihood that more will happen) or if they will seize this opportunity to build supply chains that provide the capability to predict, avoid, and thrive in a changing environment.