Is there an end in sight to all of this? Technological development is faster than ever. Year after year, there is an increasingly intense response of technological solutions to well-established human needs, influencing the way each individual communicates, learns, and thinks (except for the elderly man Đorđe from Thessaloniki). The purpose of technology is to play a significant role in improving the quality of human life.
Today, in the 21st century, technology is much more than that. As solutions make their way directly to us through the numerous offerings of technological giants, they also integrate with our needs through the services of companies and their operations. Considering the pressure of innovation and the needs of new generations, companies have been taking measures for years to outsmart their competitors and maintain a leading position in the game where the sky is the limit. To better keep up with the outcomes of better, faster, and more efficient company measures, humanity has created segments of revolutionary epochs, and today, we live in the fourth industrial revolution in the field of production systems, known as Industry 4.0.
Historically, each revolution has brought something to the production sector. Starting at the end of the 18th century, the first industrial revolution introduced a production facility that used the power of water and steam, increasing human productivity eightfold. Then, at the beginning of the 20th century, in the era of Fordism, humanity promoted a capitalist society by introducing the standardization of massive and linear production systems. Soon after, in the 1970s, there was the development of semi-automatic production facilities using electronics and IT solutions—the third industrial revolution. And here we are today in 2022. What is Industry 4.0, and what has the fourth industrial revolution changed?
The term Industry 4.0 was first introduced in 2011 at a trade fair in Hanover, where a working group of the German government highlighted it as a reversal of the conventional logic of the production process. This concept is characterized by technological solutions that enable better management of production systems, production flexibility, and modern product distribution.
Cyber-physical systems, as the foundation of Industry 4.0, use modern software management systems with internet addresses for connectivity and addressing via the Internet of Things (IoT). With these technologies, products and production assets become interconnected and can "communicate," enabling new methods of production and real-time optimization. By combining the development of five core technologies that support the growth of Industry 4.0, new opportunities in this field will be unlocked. Specifically, the technologies present in today's smart factories driving this industry are primarily IoT solutions, artificial intelligence, interfaces, advanced robotics, and 3D printing. In practice, we now have smart factories equipped with advanced sensors, embedded software, and robotics that collect and analyze data, enabling better decision-making. Additionally, these solutions reach their full potential when data from production operations are combined with operational data from ERP, supply chain, customer service, and other enterprise systems, leading to entirely new levels of analysis and insights from previously isolated information.
Some of the expected outcomes of such an industrial transformation include a 15-20% reduction in inventory costs, a 15-30% increase in productivity, a 30-50% reduction in machine downtime, and an 85% improvement in prediction accuracy.
A good example of a company that has successfully implemented smart factory integration, somewhat expected, comes from the automotive industry. Seat, for instance, has undergone a digital transformation in its Martorell plant, where, alongside numerous benefits of digitalization and connection to Volkswagen's digital production platform, the most prominent is the calculated maintenance prediction of the entire facility by 2025.
However, in the midst of a crisis that has affected the entire world, this type of transformation is a challenge, even for the largest companies. On the one hand, leaders have faced the impacts of COVID-19, which are well-known to all of us, while on the other hand, there are global influences that have prompted these same leaders to prepare for a period of recession and inflation. In both cases, as companies contemplate rebuilding their operations to cope with crises, the use of digital technologies will be paramount for many.
When it comes to manufacturing companies and their digital transformation of the operational model, we can confidently say that every step towards digital business represents a step towards Industry 4.0. Therefore, it is essential to clearly define a company's strategic path to efficiently reach its full potential. As the foundation of the strategy, I would highlight five key segments integrated into the dynamics of the market and the ecosystem focused on Industry 4.0, as well as the opportunities to strive for.
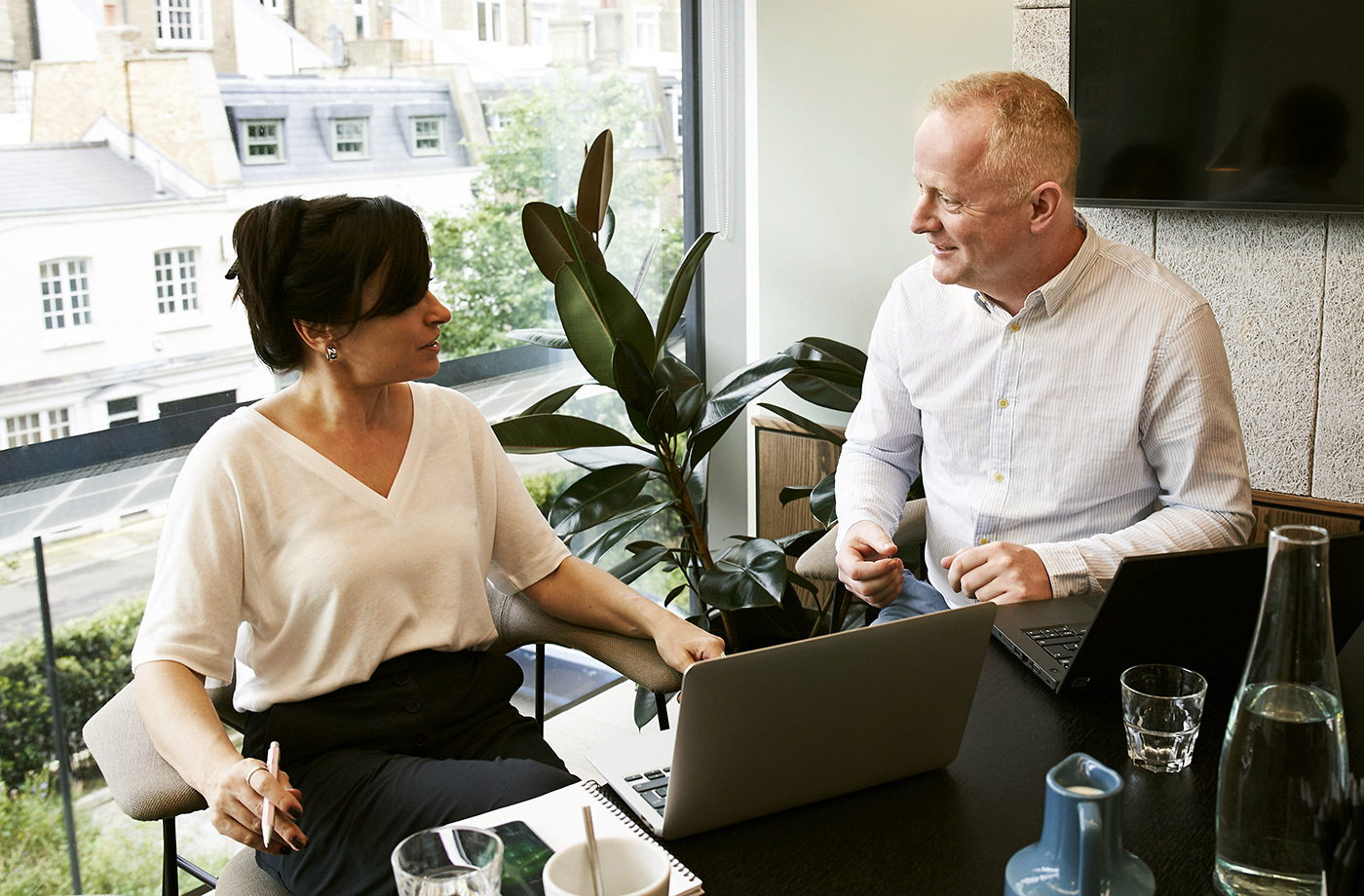
Customer-Centric Flexibility
When it comes to customer-centricity, where customers frequently change their demands under the influence of market trends, flexibility represents a significant comparative advantage. For such a company, it is essential to have the ability to individually adapt products and production volumes to customer preferences. In this case, there are numerous solutions that enable such flexibility, such as order handling automation, flexible production systems, adaptive logistics, and more.
Operational Excellence
Within operational excellence, I particularly like to emphasize increasing productivity through continuous and dynamic optimization of all processes along the value chain to achieve efficiency in line with customer requirements, which is crucial to implement during the technological transition. Technologies supporting such changes are generally based on real-time automated production management and process control, improving the productivity of employees and synchronizing product design and production.
Environment, Safety, and Health
In order to promote human values and establish a corporate culture that nurtures a healthy working environment during the transition to Industry 4.0, solutions aimed at HR activities that focus on improving ergonomics and safety at work, as well as reducing resource and energy consumption, should be sought.
People
According to the Education Commission, it is predicted that by 2030, more than half of nearly two billion young people worldwide will lack the skills or qualifications necessary to participate in the global workforce in development. In practical terms, this means that more than 50% of tomorrow's human capital may not be prepared to keep up with the development of the skills required for future jobs. Therefore, companies must find a way to develop their employees through education and prepare them for the needs of the new industrial revolution.
Solutions
The aforementioned segments, depending on the industry, can have different interpretations and elaborations to the level of specific activities. There are four foundations when implementing technological transformation towards Industry 4.0, consisting of integrated IT/cloud platforms, machine communication with the cloud, an operational model for overall alignment, and potential partnerships for additional opportunities. In the end, it is essential to emphasize that company leadership must define specific goals to strive for, break them down into specific project initiatives in line with priorities, and determine the technological solutions needed to efficiently carry out the transformation because the better prepared they are, the longer they will endure this technological marathon.